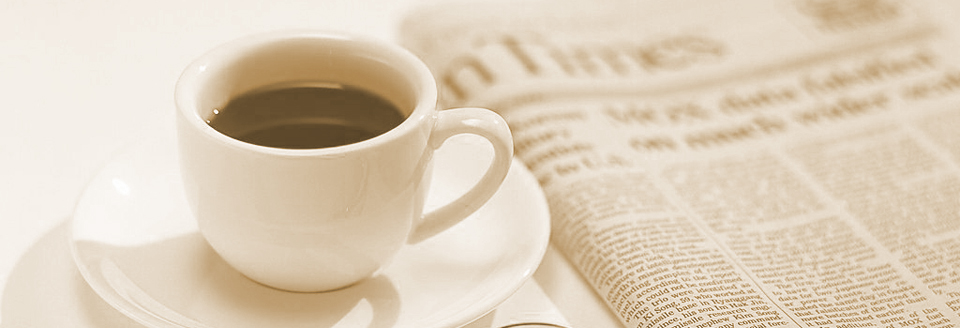
當(dāng)前位置:希尼爾首頁 > 專業(yè)詞匯
> 商貿(mào)英語 > 企業(yè)資源計劃(ERP)專業(yè)術(shù)語 - 中英對照
企業(yè)資源計劃(ERP)專業(yè)術(shù)語 -中英對照
From:青島希尼爾翻譯公司 http://m.shreekrishnajewellers.com
企業(yè)資源計劃(ERP)專業(yè)術(shù)語
A
ABC Classification——ABC分類法
對于庫存的所有物料,按照全年貨幣價值從大到小排序,然后劃分為三大類,分別稱為A類、B類和C類。A類物料價值最高,受到高度重視,處于中間的B類物料受重視程度稍差,而C類物料價值低,僅進行例行控制管理。ABC分類法的原則是通過放松對低值物料的控制管理而節(jié)省精力,從而可以把高值物料的庫存管理做得更好。
Abnormal Demand——反常需求
Action Message——措施信息
MRP II系統(tǒng)的一類輸出信息,說明為糾正現(xiàn)存問題或潛在問題需要采取的措施及措施類型。例如,“下達訂單”、“重新排產(chǎn)”、“取消”等。
Action-report-flag——活動報告標(biāo)志
Activity-based Costing (ABC)——基于活動的成本核算
進行成本核算時,對已完成的活動所發(fā)生的成本,先進行累計,再把總成本按照產(chǎn)品種類、顧客群、目標(biāo)市場或者項目課題進行分?jǐn)?。這一核算系統(tǒng)所應(yīng)用的成本核算基礎(chǔ),較之把總成本分?jǐn)偟街苯尤斯ず蜋C器工時的方法,更加貼近實際情況。也稱為吸收式成本核算(Absorption
Costing)。
Actual Capacity——實際能力
Actual Costs——實際成本
Adjust-on-hand——調(diào)整現(xiàn)有庫存量
Allocation——已分配量
在MRP II系統(tǒng)中,已分配物料是指已向庫房發(fā)出提貨單,但尚未由庫房發(fā)貨的物料。已分配量是尚未兌現(xiàn)的庫存需求。
Alternative Routine——替代工序
Anticipated Delay Report——拖期預(yù)報
一種由生產(chǎn)和采購部門向物料計劃部門發(fā)出的報告,說明哪些生產(chǎn)任務(wù)或采購合同不能按期完成、原因何在以及何時可以完成。拖期預(yù)報是閉環(huán)MRP
系統(tǒng)的基本組成部分。除了特別大的公司以外,拖期預(yù)報一般由人工編制。
Assembly——裝配
Assembly Order——裝配訂單
Assembly Parts List——裝配零件表
Automatic Rescheduling——計劃自動重排
允許計算機系統(tǒng)當(dāng)它發(fā)現(xiàn)交貨日期和需用日期失效時,自動改變預(yù)計入庫量的交貨日期。一般不推薦這種方法。
Available Material——可用材料
Available Inventory——可達到庫存
Available Stock——達到庫存
Available Work——可利用工時
Available-to-promise——可簽約量
公司庫存量或計劃生產(chǎn)量中尚未簽約的部分。這種數(shù)字通??捎芍魃a(chǎn)計劃計算出來,并作為簽訂銷合同的依據(jù)而不斷調(diào)整。
Average Inventory——平均庫存
B
Backflush——倒沖法
根據(jù)已生產(chǎn)的裝配件產(chǎn)量,通過展開物料清單,將用于該裝配件或子裝配件的零部件或原材料數(shù)量從庫存中沖減掉。
Backlog——未完成訂單
所有已收到但尚未發(fā)貨的客戶訂單。也稱為未結(jié)訂單。
Back Scheduling——倒序計劃
計算開工日期及完工日期的一種方法。生產(chǎn)計劃的計算由合同的交貨日期開始,進行倒序計算,以便確定每道工序的完工日期。
Back Order——欠交訂單
Balance-on-hand Inventory——現(xiàn)有庫存余額
Batch Number——批號
Batch Production——批量生產(chǎn)
Benchmarking——標(biāo)桿瞄準(zhǔn)
指企業(yè)將自己的產(chǎn)品、服務(wù)、成本和經(jīng)營實踐,與那些相應(yīng)方面表現(xiàn)最優(yōu)秀、最卓有成效的企業(yè)(并不局限于同一行業(yè))相比較,以改進本企業(yè)經(jīng)營業(yè)績和業(yè)務(wù)表現(xiàn)的這樣一個不間斷的精益求精的過程。也譯為基準(zhǔn)評價。
Bill of Labor——工時清單
Bill of Lading——提貨單
Bill of Material——物料清單
構(gòu)成父項裝配件的所有子裝配件、中間件、零件及原材料的清單,其中包括裝配所需的各子項的數(shù)量。物料清單和主生產(chǎn)計劃一起作用,來安排倉庫的發(fā)料、車間的生產(chǎn)和待采購件的種類和數(shù)量??梢杂枚喾N方法描述物料清單,如單層法、縮進法、模塊法、暫停法、矩陣法以及成本法等等。在某些工業(yè)領(lǐng)域,可能稱為“配方”、“要素表”或其他名稱。
Business Process Reengineer(BPR)——業(yè)務(wù)流程重組
Branch Warehouse——分庫
Business Plan——經(jīng)營規(guī)劃
包括預(yù)計收入、成本和利潤,通常還有預(yù)算和計劃的資產(chǎn)負(fù)債表及現(xiàn)金流量表(資金來源和資金運用)的文件。通常僅用貨幣單位表述。盡管經(jīng)營規(guī)劃和生產(chǎn)規(guī)劃以不同的術(shù)語來表述,但二者應(yīng)該是一致的。
Buyer——采購員
C
Capacity Management——能力管理
指企業(yè)管理活動中,為更好地執(zhí)行所有的生產(chǎn)進度安排,建立生產(chǎn)能力的限額或水平并對其進行度量、監(jiān)控及調(diào)整的職能。具體如生產(chǎn)計劃、主生產(chǎn)計劃、物料需求計劃和派工單等等。能力管理體現(xiàn)在資源計劃、粗能力計劃、能力需求計劃和投入/產(chǎn)出控制等四個層次。
Capacity Requirements Planning (CRP)——能力需求計劃
確定為完成生產(chǎn)任務(wù)具體需要多少勞力和機器資源的過程。在MRP系統(tǒng)中,已下達的車間訂單和計劃訂單是能力需求計劃的輸入。能力需求計劃將這些訂單轉(zhuǎn)換成不同時區(qū)、不同工作中心上的工時數(shù)。有時會出現(xiàn)這樣的情況,粗能力計劃分析認(rèn)為企業(yè)的現(xiàn)有生產(chǎn)能力足以完成主生產(chǎn)計劃,而能力需求計劃經(jīng)過更細(xì)致的分析,得出在某些時段生產(chǎn)能力不足的結(jié)論。
Carrying Cost——保管費
Carrying Cost Rate——保管費率
Cellular Manufacturing——單元式制造
指在一條生產(chǎn)線或一個機器設(shè)備單元內(nèi),由本生產(chǎn)線或生產(chǎn)單元的操作工生產(chǎn)多種產(chǎn)品或零部件的生產(chǎn)制造過程。
Change Lot Date——修改批量日期
Change Structure——修改產(chǎn)品結(jié)構(gòu)
Change Route——修改工序
Check Point——檢查點
Closed Loop MRP——閉環(huán)物料需求計劃
圍繞物料物料需求計劃而建立的系統(tǒng),包括生產(chǎn)規(guī)劃、主生產(chǎn)計劃和能力需求計劃與其他計劃功能。進一步地,當(dāng)計劃階段完成并且作為實際可行的計劃被接收以后,執(zhí)行階段隨之開始。這包括投入/產(chǎn)出控制、車間作業(yè)管理、派工單以及來自車間及供應(yīng)商的拖期預(yù)報?!伴]環(huán)”一詞所指的,不僅包括整個系統(tǒng)的這些組成部分,并且還包括來自執(zhí)行部分的反饋信息,目的在于使計劃在任何時候都保持有效。
Common Route ID——通用工序標(biāo)識
Computer-integrated Manufacturing (CIM)——計算機集成制造
利用計算機系統(tǒng)和管理哲學(xué),將整個生產(chǎn)制造組織集成為一體,以提高組織運作效率。也指應(yīng)用一臺計算機,把原先相互獨立的不同計算機系統(tǒng)聯(lián)通成為一個內(nèi)部一致、高度集成的整體。例如,計算機集成制造技術(shù)可以實現(xiàn)預(yù)算規(guī)劃、CAD/CAM、流程控制、成組技術(shù)系統(tǒng)、MRP
II以及財務(wù)報告系統(tǒng)的相互溝通。
Configuration Code——配置代碼
Constraints Management/Theory of Constraints (TOC)——約束管理/約束理論
簡單的講,約束理論是關(guān)于企業(yè)應(yīng)作哪些變化以及如何最好地實現(xiàn)這些變化的理論。具體一些,約束理論是這樣一套管理原則──幫助企業(yè)找出目標(biāo)實現(xiàn)過程中存在的障礙,并實施必要的改變來消除這些障礙。約束理論認(rèn)為,對于任何一個系統(tǒng)來說,如果它的投入/產(chǎn)出過程可以按環(huán)節(jié)或者階段進行劃分,而且一個環(huán)節(jié)的產(chǎn)出依賴于前面一個或多個環(huán)節(jié)的產(chǎn)出的話,那么,這個系統(tǒng)最終的產(chǎn)出將受到系統(tǒng)內(nèi)生產(chǎn)率最低的環(huán)節(jié)的限制。換言之,任何一個鏈條的牢固程度取決與它最薄弱的環(huán)節(jié)。
在論及生產(chǎn)制造企業(yè)時,約束理論認(rèn)為企業(yè)的目標(biāo)就是取得更多的利潤。為實現(xiàn)這一目標(biāo),可以有三條途徑:增加產(chǎn)銷率,減少庫存,減少運營費用。這三條途徑中,正如約束理論奠基者Dr.
Goldratt所說,減少庫存和減少運營費用會碰到最低減少到0的限制,而對于通過提高產(chǎn)銷率來取得更多利潤的可能性,則是無窮無盡的。此外,約束理論還發(fā)展出一系列工具,來幫助企業(yè)重新審視自己的各種行為和措施,看它們對于企業(yè)目標(biāo)的實現(xiàn)產(chǎn)生了怎樣的有利或不利的影響。
Costed Bill of Material——依成本的材料清單
Critical Part——急需零件
Cumulative Lead Time——累計提前期
指完成某項活動的最長時間。對于任一MRP計劃物料項目來說,其累計提前期可以通過遍歷該項物料的物料清單中各條路徑來得到,即將各路徑上所有低層次項目提前期的最大累計值定義為該項目的累計提前期。也稱為合成提前期或關(guān)鍵路徑提前期。
Current Run Hour——現(xiàn)有運轉(zhuǎn)時間
Current Run Quantity——現(xiàn)有運轉(zhuǎn)數(shù)量
Cycle Counting——周期盤點
一種庫存盤點方法。庫存按計劃定期盤點,而不是一年才盤點一次。例如,某種物料的庫存達到訂貨點時,或新物料到庫時都可以進行盤點。也可以事先訂立某種一貫的盤點原則,比如對價值高并且流動快的物料多盤點;對價值低或流動慢的物料少盤點。最有效的周期盤點制度要求每個工作日清點一定數(shù)目的物料。周期盤點最主要的目的是發(fā)現(xiàn)那些疵點存貨(如:存在數(shù)量、質(zhì)量、規(guī)格、日期等等方面的問題),進而追究其原因,最終消除導(dǎo)致問題產(chǎn)生的根本因素。
D
Date Adjust——調(diào)整日期
Date Available——有效日期
Date Changed——修改日期
Date Closed——結(jié)束日期
Date Due——截止日期
Date in Produced——生產(chǎn)日期
Date Inventory Adjust——庫存調(diào)整日期
Date Obsolete——作廢日期
Date Required——需求日期
Date Received——收到日期
Date Released——交付日期
Date to Pull——發(fā)貨日期
Dead Load——空負(fù)荷
Demand——需求
對指定產(chǎn)品或零部件的需要,這種需要可能來源于客戶訂單、預(yù)測、廠際訂貨、分庫、維修部門,也可能來自較高一層的零件或產(chǎn)品。
Demand Management——需求管理
指認(rèn)識和管理對產(chǎn)品的全部需求,并確保主生產(chǎn)計劃反映這些需求的功能。需求管理包括:預(yù)測、訂單錄入、訂單承諾、分庫需求、非獨立需求、廠際訂單及維修件需求等。
Demonstrated Capacity——實際能力
由實際完成數(shù)據(jù)計算出的能力。實際能力的計算通常用生產(chǎn)的項目乘上每個項目的標(biāo)準(zhǔn)工時再加上標(biāo)準(zhǔn)的準(zhǔn)備時間。
Dependent Demand——非獨立需求
當(dāng)對一項物料的需求與對其他物料項目或最終產(chǎn)品的需求有關(guān)時,稱為非獨立需求。這些需求是計算出來的而不是預(yù)測的,對于具體的物料項目,有時可能既有獨立需求又有非獨立需求。
Direct-deduct Inventory Transaction Processing——直接增減庫存處理法
指一種記帳方法,當(dāng)物料出庫時,減少該項物料的帳面(計算機內(nèi))庫存數(shù);當(dāng)物料入庫時,增加該項物料的帳面庫存數(shù)。帳面數(shù)據(jù)隨物料的出入庫同步更新。因此,帳面的庫存記錄就是實際庫存的反映。
Disbursement List——發(fā)料單
Dispatch List——派工單
根據(jù)調(diào)度原則按優(yōu)先級順序編制的生產(chǎn)訂單一覽表。利用硬拷貝或CRT顯示將派工單通知給生產(chǎn)車間。派工單中包括生產(chǎn)訂單的優(yōu)先級、物料存放地點、數(shù)量及能力需求的詳細(xì)信息,所有這些信息都是按工序排列的。派工單通常每天產(chǎn)生并按工作中心進行調(diào)整。也稱為調(diào)度表或工長日報表。
Distribution Resource Planning (DRP)——分銷資源計劃
是分銷需求計劃的延伸部分,涉及分銷系統(tǒng)中的關(guān)鍵資源(如倉儲空間、勞動力、貨幣資金、運輸工具等等)的計劃。
Drum-buffer-rope——鼓-緩沖-繩子
是在通過對資源進行計劃和控制,以實現(xiàn)產(chǎn)銷率最大化的過程中最常用的技術(shù)。瓶頸約束控制著企業(yè)的生產(chǎn)節(jié)拍和產(chǎn)出率──“鼓點”。從計劃和控制的角度來看,
“鼓”反映了系統(tǒng)對約束資源的利用程度。為充分利用瓶頸的能力,一般要設(shè)置一定的“緩沖”,來防治生產(chǎn)過程中的波動。瓶頸通過“繩子”對其上游控制物料送入的環(huán)節(jié)發(fā)出指令,使物料快速、有效地通過非瓶頸環(huán)節(jié)。所以,“繩子”起的是串聯(lián)和傳遞的作用,以驅(qū)動系統(tǒng)的所有部分按“鼓”的節(jié)奏進行生產(chǎn)。
E
Economic Order Quantity (EOQ)——經(jīng)濟訂貨批量
是固定訂貨批量模型的一種,可以用來確定企業(yè)一次訂貨(外購或自制)的數(shù)量。當(dāng)企業(yè)按照經(jīng)濟訂貨批量來訂貨時,可實現(xiàn)訂貨成本和儲存成本之和最小化?;竟绞牵?br>
經(jīng)濟訂貨批量=Squat(2*年訂貨量*平均一次訂貨準(zhǔn)備所發(fā)生成本/每件存貨的年儲存成本)注:Squat()函數(shù)表示開平方根。
Engineering Change Effect Date——工程變更生效日期
Engineering Change Effect Work Order——工程變更生效單
Engineering Stop Date——工程停止日期
Exception Control——例外控制
Excess Material Analysis——呆滯材料分析
Expedite Code——急送代碼
F
Fabrication Order——加工訂單
Fill Backorder——補足欠交
Firm Planned Order——確認(rèn)的計劃訂單
指在數(shù)量和時間上已確認(rèn)的計劃訂單。這種訂單不能由計算機改變,而只能由計劃員改變。這種做法有助于計劃員對物料和能力問題做出反應(yīng)。此外,確認(rèn)的計劃訂單還是闡明生產(chǎn)計劃的常規(guī)方法。
Final Assembly Lead Time——總裝提前期
Fixed Order Quantity——固定訂貨批量
一種批量訂貨方法,每次訂貨時都采用預(yù)先確定的同樣數(shù)量。
Flow Shop——流水車間
在這樣的車間里,機器和操作工通常處理標(biāo)準(zhǔn)的、連續(xù)的物流。操作工總是對每批生產(chǎn)任務(wù)進行同樣的操作。流水車間一般是大批量生產(chǎn)車間或具有連續(xù)生產(chǎn)布局的車間。車間的布局,即機器、工作臺及裝配線等等的排列方法,是為便于產(chǎn)品流動而設(shè)計的。流程工業(yè)(如化工、石油加工、油漆等)是流水車間的典型例子。每種產(chǎn)品,盡管材料規(guī)格不同,整個車間總是采用同樣的流程。
Focus Forecasting——調(diào)焦預(yù)測
調(diào)焦預(yù)測是一個系統(tǒng),它可以模擬并評估一系列不同的策略,然后從中選擇已被證明對于最近的過去所作的預(yù)測最為有效的預(yù)測技術(shù),用來預(yù)測未來。即使用簡單的規(guī)則,對所有的規(guī)則進行測試,選擇出對某項物料最為適合的方法,使用所選擇的方法預(yù)測未來的銷售量。
Full Pegging——完全跟蹤
指系統(tǒng)自動跟蹤給定零部件的所有需求,直到最終項目(或合同號)的能力。
G
Generally Accepted Manufacturing Practices——通用生產(chǎn)管理原則
指一整套不受具體技術(shù)影響的原則,闡明制造企業(yè)應(yīng)該如何進行管理。其中包括如下要素:對數(shù)據(jù)準(zhǔn)確性的要求,市場工作與生產(chǎn)環(huán)節(jié)的經(jīng)常聯(lián)系,高層領(lǐng)導(dǎo)對生產(chǎn)計劃過程的控制,將上層計劃有效地轉(zhuǎn)換為各種詳細(xì)計劃的系統(tǒng)能力,等等。
Gross Requirements——毛需求
I
Independent Demand——獨立需求
當(dāng)對某項物料的需求與對其他物料的需求無關(guān)時,則稱這種需求為獨立需求。例如對成品或維修件的需求就是獨立需求。
In Process Inventory——在制品庫存
Input/ Output Control投入/產(chǎn)出控制
一種能力控制技術(shù),它將工作中心的實際產(chǎn)出與由能力需求計劃產(chǎn)生并由生產(chǎn)部門批準(zhǔn)的計劃產(chǎn)出相比較。并且監(jiān)控投入,以檢查是否與計劃一致,這樣,當(dāng)工作中心不能得到加工作業(yè)時,也不期望它有產(chǎn)出。
Inspection ID——檢驗標(biāo)識
Interplant Demand廠際需求
物料需要發(fā)送到同一公司內(nèi)其他工廠或部門,雖然不是客戶訂單,但主生產(chǎn)計劃通常以同樣的方式處理。
Inventory Carry Rate——庫存周轉(zhuǎn)率
Inventory Location Type——倉庫庫位類型
Inventory Turnover——庫存周轉(zhuǎn)次數(shù)
一年中存貨流動或循環(huán)的次數(shù),是對為支持一定水平的銷售活動的庫存投資的度量。計算方法是用全年售出貨物成本除以平均存貨價值。
Issue Order——發(fā)送訂單
Item——物料項目
任何一種自制或采購的零部件或組裝件,如最終產(chǎn)品、部件、子部件、零件或原材料。
Item Record——項目記錄
即物料項目的主記錄,一般包括標(biāo)識數(shù)據(jù)和描述數(shù)據(jù)以及控制參數(shù)(各種提前期、訂貨批量等等)。也可能還有庫存狀態(tài)、需求及計劃訂貨數(shù)據(jù)。項目記錄通過物料清單(或稱產(chǎn)品結(jié)構(gòu)文件)聯(lián)系在一起。
J
Job Shop——加工車間
一種職能單位,它的工段或工作中心是圍繞著不同類型設(shè)備或工序來組織的,如鉆床、鍛壓機、車床、裝配線等。
Just-in-time (JIT)——準(zhǔn)時制生產(chǎn)
指建立在力求消除一切浪費和不斷提高生產(chǎn)率基礎(chǔ)上的一種生產(chǎn)理念。它覆蓋了從產(chǎn)品設(shè)計直到產(chǎn)成品發(fā)送一整套的生產(chǎn)活動。只要這些活動是出產(chǎn)一件最終產(chǎn)品所需要的,包括從原材料開始的各個在制品生產(chǎn)階段,都必須向消除一切浪費、不斷提高生產(chǎn)率的目標(biāo)看齊。
準(zhǔn)時制生產(chǎn)的主要思想有:盡可能地減少庫存;產(chǎn)品質(zhì)量追求零缺陷;通過縮短調(diào)整準(zhǔn)備時間、等待隊列長度,減少批量等來壓縮提前期等等。
狹義上指在需要的時間把物料送達需要的地方。它的實施是每道工序都與后續(xù)的工序同步,以使庫存最少。
廣義上適用于加工車間、流程生產(chǎn)以及重復(fù)型生產(chǎn)等所有生產(chǎn)類型。與“短周期生產(chǎn)”、“無庫存生產(chǎn)”、“零庫存”意義類似。國內(nèi)文獻有時也譯作“及時生產(chǎn)”。
K
Kanban——看板
是個日語名詞,表示一種掛在或貼在盛裝在制品的容器上或一批零件上的標(biāo)簽或卡片,或流水線上各種顏色的小球或信號燈、電視圖象等??窗迨墙沂九?,可以作為交流廠內(nèi)生產(chǎn)管理信息的手段??窗蹇ㄆ喈?dāng)多的信息并且可以反復(fù)使用??窗逋ǔJ茄b在透明的長方形乙烯封套中,為得是在工廠環(huán)境中保護卡片不受損壞。
常用的看板有兩種:生產(chǎn)看板(或生產(chǎn)通知看板)和運送看板(或取貨看板)。生產(chǎn)看板指在一個工廠內(nèi),指示某工序加工制造規(guī)定數(shù)量工件所用的看板。運送看板是指后道工序的操作者按看板上所列件號,到前到工序(或協(xié)作廠)領(lǐng)取的看板。
L
Labor Hour——人工工時
Last Shipment Date——最后運輸日期
Lead Time——提前期
完成一項活動所需要的時間。這種活動通常指物料和產(chǎn)品的獲得,無論是從外面購入的還是用自己的設(shè)備制造的。提前期可由下列各種時間或它們的總和組成:訂單準(zhǔn)備時間、排隊時間、加工時間、搬運時間或運輸時間、接收和檢測時間。
Level——層
在產(chǎn)品結(jié)構(gòu)中,每個零件都被指定一個層次代碼,標(biāo)識該零部件的相對層次。通常,最終產(chǎn)品被指定為0層,直接組成它的部件被指定為1層,依此類推。MRP展開從0層開始,每次向下展開一層。
Line Item——單項產(chǎn)品
Load——負(fù)荷
在加工之前所計劃的工作量,常以工時或產(chǎn)品件數(shù)表示。
Load Leveling——負(fù)荷量
Load Report——負(fù)荷報告
Location Code——倉位代碼
Location Remarks——倉位備注
Location Status——倉位狀況
Lot ID——批量標(biāo)識
Lot Number——批量編號
Lot Size——批量
Lot for Lot——按需訂貨
MRP的一種訂貨技術(shù),生成的計劃訂單在數(shù)量上等于每個時間段的凈需求量。
Low Level Code低位碼
M
Machine Capacity——機器能力
Machine Loading——機器加載
對某時間段內(nèi)下達的訂單,由工序計劃產(chǎn)生工時數(shù),然后按工作中心進行累加。機器加載不同于能力需求計劃,它不使用來自MRP的計劃訂單,而只處理關(guān)于預(yù)計入庫量的訂單。因此,它的作業(yè)是有限的。
Make or Buy Decision——外購或自制決策
Make-to-order Product——面向訂單生產(chǎn)的產(chǎn)品
最終產(chǎn)品在收到客戶訂單后才能確定。為了縮短向客戶的交貨期,對于具有較長提前期的零部件要在訂單到達之前做出計劃。對于選件或其它子部件在客戶訂單到達之前已經(jīng)存放在倉庫里。這種生產(chǎn)方式,通常也稱為按訂單裝配或訂貨生產(chǎn)。
Make-to-stock Product——面向庫存生產(chǎn)的產(chǎn)品
最終產(chǎn)品是從成品庫中直接發(fā)運的,因此在客戶訂單到達之前已經(jīng)制成。也稱為備貨生產(chǎn)產(chǎn)品。
Manufacturing Cycle Time——制造周期時間
Manufacturing Resource Planning (MRP II)——制造資源計劃
對于制造企業(yè)的所有資源進行有效計劃的一種方法。MRP
II包括許多相互聯(lián)系的功能:經(jīng)營規(guī)劃、生產(chǎn)規(guī)劃、主生產(chǎn)計劃、物料需求計劃、能力需求計劃以及有關(guān)能力和物料的執(zhí)行支持系統(tǒng)。這些系統(tǒng)的輸出與各種財務(wù)報告集成在一起。制造資源計劃是閉環(huán)MRP的直接發(fā)展和延伸。MRP
II也稱為基于網(wǎng)絡(luò)計劃的管理系統(tǒng)。
Master Production Schedule (MPS)——主生產(chǎn)計劃
預(yù)先建立的一份計劃,由主生產(chǎn)計劃員負(fù)責(zé)維護。主生產(chǎn)計劃是驅(qū)動MRP的一整套計劃數(shù)據(jù),它反映出企業(yè)打算生產(chǎn)什么,什么時候生產(chǎn)以及生產(chǎn)多少。主生產(chǎn)計劃必須考慮客戶訂單和預(yù)測、未完成訂單、可用物料的數(shù)量、現(xiàn)有能力、管理方針和目標(biāo)等等。
Material Cost——物料成本
Material Issues and Receipts——物料發(fā)送和接收
Material Requirements Planning (MRP)——物料需求計劃
利用物料清單、庫存數(shù)據(jù)和主生產(chǎn)計劃計算物料需求的一套技術(shù)。物料需求計劃產(chǎn)生下達補充物料清單的建議,而且由于它是劃分為時間段的,當(dāng)?shù)截浫掌谂c需求日期不同步時,
MRP會建議重排未結(jié)清單。最初MRP只被看成一種比庫存訂貨點更好的庫存管理方法,現(xiàn)在普遍認(rèn)為它是一種計劃技術(shù),即建立和維護訂單的有效到貨日期的方法,它是閉環(huán)MRP的基礎(chǔ)。
MPS Book Flag——MPS登陸標(biāo)志
Multiple Location——多重倉位
N
Net Change MRP——凈改變式MRP
計算機處理物料需求計劃的一種方法。物料需求計劃連續(xù)保留在計算機里。當(dāng)需求、未結(jié)訂單、庫存狀態(tài)或物料清單等有所改變時,則僅對受這些改變影響的零部件進行需求展開重排。
Net Requirements——凈需求
在MRP里,物料的凈需求是通過毛需求減去現(xiàn)有庫存量和預(yù)計入庫量計算出來的,根據(jù)凈需求、訂貨批量和提前期偏置即可構(gòu)成計劃訂單。
New Location——新倉位
New Parent——新組件
New Warehouse——新倉庫
No Action Report——不活動報告
O
On-hand Balance——現(xiàn)有庫存量
庫存記錄所顯示的實際存儲在倉庫里的物料數(shù)量。
Open Order——未結(jié)訂單
指尚未完成的生產(chǎn)訂單或采購訂單。
Order Entry——訂單輸入
接收客戶訂單并把客戶所需要的東西轉(zhuǎn)換為企業(yè)慣用的術(shù)語的過程,最簡單的情況是生成成品的發(fā)貨文件,較為復(fù)雜的情況是描述包括按訂單生產(chǎn)產(chǎn)品的工程要求的一系列活動。
Order Point——訂貨點
Order Policy——訂貨方針
Order Remarks——訂貨備注
Order Promising——訂貨承諾
給出發(fā)貨承諾的過程?;卮鹬T如什么時候可以發(fā)貨之類的問題。對于面向訂單生產(chǎn)的產(chǎn)品,訂貨承諾通常涉及到對物料和能力的檢查。
P
Parent——雙親
Part——零件
Part Bills——零件清單
Part Number——零件編號
Part Lot——零件批次
Pegging——反查
在MRP中,對于某個指定的物料項目,通過反查顯示該項物料的毛需求及已分配量的來源的詳細(xì)情況。所以,反查是給出物料實際用在哪里的信息。
Picking——領(lǐng)料/提貨
為制造產(chǎn)品從庫存中領(lǐng)取原材料或零部件,或者為了向客戶發(fā)貨從庫存中提取完工產(chǎn)品的過程。
Picking List——領(lǐng)料單
標(biāo)識所需要的零部件或完工產(chǎn)品名稱及數(shù)量,作為領(lǐng)料或提貨依據(jù)的文件。
Planned Order——計劃訂單
當(dāng)出現(xiàn)凈需求時,MRP即生成訂貨數(shù)量和交貨日期的建議,即計劃訂單。計劃訂單由計算機生成并且僅存放于計算機中,如果條件發(fā)生變化,下次MRP處理可能改變或刪除原來的計劃訂單。處于某一層的計劃訂單將分解成下一個低層物料的毛需求。計劃訂單與預(yù)計入庫量也是能力需求計劃的輸入,用以計算出未來時區(qū)內(nèi)的能力總需求。
Post-deduct Inventory Transaction Processing——后減庫存處理法
一種庫存記帳方法。物料項目的帳面(存于計算機中)庫存量是在其父項或裝配件的活動完成之后才被減去。這種方法的缺點是帳面記錄與實際庫存經(jīng)常不一致。這種方法也稱為倒沖法。
Pre-deduct Inventory Transaction Processing——前減庫存處理法
一種庫存記帳方法。物料項目的帳面(存于計算機中)庫存量在發(fā)料之前,即對其父項或裝配件產(chǎn)生預(yù)計入庫量之時即被減去。這種方法的缺點是帳面記錄與實際庫存經(jīng)常不一致。
Price Invoice——發(fā)票價格
Price Purchase Order——采購訂單價格
Priority Planning——優(yōu)先計劃
Product Control——產(chǎn)品控制
Production Line——產(chǎn)品線
Production Rate——產(chǎn)品率
Production Tree——產(chǎn)品結(jié)構(gòu)樹
Production Planning——生產(chǎn)規(guī)劃編制
是確定企業(yè)產(chǎn)出整體水平的功能。其主要目的是通過提高或降低庫存或未完成訂單水平來確定可以達到管理目標(biāo)的生產(chǎn)率,同時要努力保持生成均衡。生產(chǎn)規(guī)劃通常是用產(chǎn)品類來表述的。必須為足夠長的計劃期作出關(guān)于勞力、設(shè)備、工具、物料和資金的計劃,以便實現(xiàn)整體管理目標(biāo)。在不同的企業(yè)中可以用不同的計量單位來表述生產(chǎn)規(guī)劃,諸如標(biāo)準(zhǔn)小時、噸位、工人數(shù)、臺、件、貨幣單位等等。由于這個規(guī)劃影響企業(yè)的所有業(yè)務(wù),所以,它的編制必須要有來自市場、制造、工程技術(shù)、財務(wù)、物料等方面的信息。然后,生產(chǎn)規(guī)劃成為編制更詳細(xì)的計劃的依據(jù)。
Projected Available Balance——預(yù)計可用庫存
預(yù)計未來可用的庫存。計算公式是:現(xiàn)有庫存量-需求量+預(yù)計入庫量+計劃訂貨量。
Purchase Order Tracking——采購訂單跟蹤
Q
Quantity Allocation——已分配量
Quantity At Location——倉位數(shù)量
Quantity Backorder——欠交數(shù)量
Quantity Completion——完成數(shù)量
Quantity Demand——需求量
Quantity Gross——毛需求量
Quantity In——進貨數(shù)量
Queue——隊列
指在生產(chǎn)過程中,在某一工作中心等待處理的那些作業(yè)。當(dāng)隊列增大時,平均提前期及在制品庫存也將增大。
Queue Time——排隊時間
工作開始之前,作業(yè)在某一工作中心等待的時間。排隊時間是整個生產(chǎn)提前中的一部分,排隊時間的增加會導(dǎo)致生產(chǎn)提前期的增加。
R
Regenerated MRP——重生成式MRP
在計算機里處理MRP的一種方法。它將主生產(chǎn)計劃依照物料清單全部重新展開,一般每周一次,以維護優(yōu)先級的有效性。此時,新需求和計劃訂單完全是重新生成的。
Rescheduling Assumption——重排假設(shè)
MRP的基本邏輯之一,它假設(shè)在短期內(nèi)重排現(xiàn)存的未結(jié)訂單比下達和接收新訂單容易得多。因此,將所有預(yù)計入庫量全部用于覆蓋毛需求之后,才生成新的計劃訂單。
Resource Requirements Planning——資源需求計劃
見Rough-cut Capacity Planning(粗能力計劃)
Rough-cut Capacity Planning——粗能力計劃
將生產(chǎn)規(guī)劃或主生產(chǎn)計劃轉(zhuǎn)換成對主要資源的能力需求的過程,包括勞動力、設(shè)備、庫存空間及供應(yīng)商的能力,有時還要考慮資金能力。通常利用生產(chǎn)負(fù)荷圖來完成這項工作。編制粗能力需求計劃的目的在于在實施計劃之前對該計劃做出評估。有時也稱為資源需求計劃。
Routing——工藝路線
詳細(xì)描述某項目制造過程的文件。包括要進行的加工及其順序。涉及到的工作中心以及準(zhǔn)備和加工所需的工時定額。在有些企業(yè)里,工藝路線還包括工具、操作工技術(shù)水平、檢驗及測試的需求等等。
S
Safety Stock——安全庫存量
是為應(yīng)付由于供需波動而發(fā)生的意外需求而設(shè)置的庫存量。
Safety Time——保險期
MRP采用的一種方法,要使物料的到達日期早于需求日期。需求日期與計劃入庫期之差即為保險期。
Scheduled Receipt——預(yù)計入庫量
在MRP
中,未完成的生產(chǎn)訂單及未到貨的采購訂單都被認(rèn)為是到貨日期的“預(yù)計入庫量”,并作為屆時可用的庫存的一部分來處理。計劃接收日期和數(shù)量一般不會被計算機自動改變。而且不對預(yù)計入庫量展開,因為根據(jù)MRP的邏輯,已假定制造這些項目所需要的零部件已分配好了,或者是已事先到達了車間的。
Scrap Factor——殘料率
MRP使用的一個百分?jǐn)?shù)??紤]到生產(chǎn)過程中某項物料的預(yù)期損失,而增加該項物料的毛需求。也稱為廢品系數(shù)。
Send Part——發(fā)送零件
Service Parts——維修件
用于維修產(chǎn)品的零件。
Ship Date——發(fā)貨零件
Ship Address——發(fā)貨地址
Ship Contact——發(fā)貨單聯(lián)系人
Ship Order——發(fā)貨單
Shop Calendar——工廠日歷
Shop Floor Control——車間作業(yè)管理
利用來自車間的數(shù)據(jù)及其它數(shù)據(jù)處理文件,維護和傳送生產(chǎn)訂單及工作中心各種狀態(tài)信息的系統(tǒng)。車間作業(yè)管理的子功能有:安排各項生產(chǎn)訂單的先后順序;維護在制品的數(shù)量信息;傳遞生產(chǎn)訂單狀態(tài)信息;為能力控制提供實際投入和產(chǎn)出數(shù)據(jù);為庫存和財務(wù)核算提供按地點及生產(chǎn)訂單分類的在制品數(shù)量信息;衡量勞動力和機器設(shè)備的有效性、利用率和生產(chǎn)率、
Shrinkage Factor——損耗系數(shù)
用于物料需求計劃中的一個百分?jǐn)?shù),用來彌補生產(chǎn)過程中預(yù)計的物料損耗。通過增加毛需求量或減少計劃訂單和未結(jié)訂單的預(yù)期完工產(chǎn)品數(shù)量來實現(xiàn)。這個損耗系數(shù)與廢品系數(shù)不同,前者影響到所用的全部物料項目,而后者只關(guān)系到某一項物料。
Standard Product Cost——標(biāo)準(zhǔn)產(chǎn)品成本
Standard Set Up Hour——標(biāo)準(zhǔn)機器設(shè)置工時
Standard Unit Run Hour——標(biāo)準(zhǔn)單位運轉(zhuǎn)工時
Standard Wage Rate——標(biāo)準(zhǔn)工資率
Status Code——狀況代碼
Stores Control——庫存控制
Suggested Work Order——建議工作單
T
Theory of Constraints (TOC)——約束理論見Constraints Management(約束管理)
Time Bucket——時間段
數(shù)據(jù)匯總的天數(shù)。在MRP中以周為時間段則按周匯總所有計劃數(shù)據(jù)。一般認(rèn)為,以 周為時間段運行MRP是最有效的(至少從近期和中期來看是如此)。
Time Fence——時界
指明操作過程中各種約束條件或改變將會發(fā)生的時間界限。例如,對于主生產(chǎn)計劃的改變在提前期之后進行則是容易的,而在累計提前期之后進行則是困難的。為此設(shè)定一個時界來限制這種改變。MRO系統(tǒng)所用的時界有計劃時界和需求時界。
U
Unit Cost——單位成本
V
Vendor Scheduler——采購計劃員
主要工作是與供應(yīng)商打交道、負(fù)責(zé)確定什么時候需要采購什么物料的人員。采購計劃員直接與MRP和供應(yīng)商接觸,他們制定物料采購計劃,交給供應(yīng)商并追蹤其表現(xiàn),解決實際問題等等。和采購員一樣,采購計劃員通常是按商品組織起來的。有了采購計劃員,就可以使采購員從天天接單、發(fā)單的工作中解脫出來,去從事降低成本、談判、選擇供應(yīng)商和貨源等更有意義的工作。
Vendor Scheduling——采購計劃法
是一種采購方法。它提供給供應(yīng)商一份采購計劃而不是一份份的訂單。通常,采購計劃系統(tǒng)包括與每個供應(yīng)商的合同、按周表述的對每個供應(yīng)商未來一段時間的采購計劃以及采購計劃員。使用這種方法,定期向供應(yīng)商提供有效的交貨日期是至關(guān)重
要的,所以這是一個正規(guī)的優(yōu)先級系統(tǒng)。
W
Work Center——工作中心
能夠完成相類似的加工操作的一組機器設(shè)備或人員,能夠被能力需求計劃作為一個單元來考慮。
Work Center Capacity——工作中心能力
Work in Process——在制品
指生產(chǎn)過程中各個階段上的產(chǎn)物,包括已下達進行粗加工的原材料和加工完畢、等待最后檢測和驗收,以便作為成品入庫或發(fā)運給客戶的產(chǎn)品。許多財務(wù)系統(tǒng)將半成品和部件也包括在這個范疇里。
Work Order——工作令
Work Scheduling——工作進度安排
Work Order Tracking——工作令跟蹤
Z
Zero Inventories——零庫存
美國生產(chǎn)和庫存控制協(xié)會(APICS,American Production & Inventory Control
Society)采用的一個術(shù)語,其意義類似于準(zhǔn)時制生產(chǎn)。